Service & Repair Partner
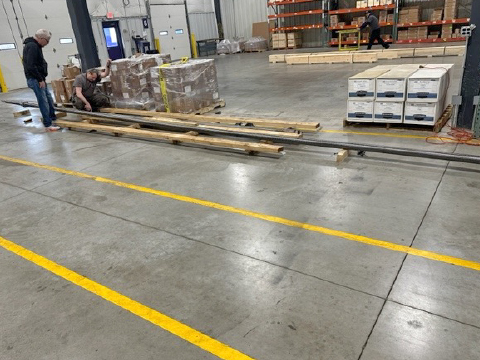
Challenge
Downtime in manufacturing can be a killer. Every minute a machine is out of commission means lost production and lost revenue – making it crucial to have a reliable and responsive maintenance partner in place.
Recently, a company that produces precision machined parts experienced a major setback when one of their production machines went down. The problem was with the ball screw, a key component that drives the movement of the machine's cutting tools. The ball screw had failed, rendering the machine out of commission until a repair solution could be arranged.
The ball screw assembly in question was 65 feet long where the screw unit was spliced, and the two halves were bent. Additionally, the drive-side diameters were broken off.
The customer had been to other repair companies and was turned away. That's when they turned to Rockford Ball Screw, a ball screw repair specialist.
Solution
The RBS repair team quickly diagnosed the problems and recommended complete replacement. But with lead time for a new screw this size being a minimum of months, the team became determined to find another way to repair the screw.
The ball screw was disassembled, cleaned, and fully inspected. New journals were manufactured and installed on the original shaft unit and the broken areas where the screw was spliced was fixed. Then the ball nut was rebuilt and sized for the existing thread conditions. From the time the purchase order was received, the team was able to make the repairs within two and a half weeks.
In all, the repair saved this company thousands of dollars and potentially months of downtime.
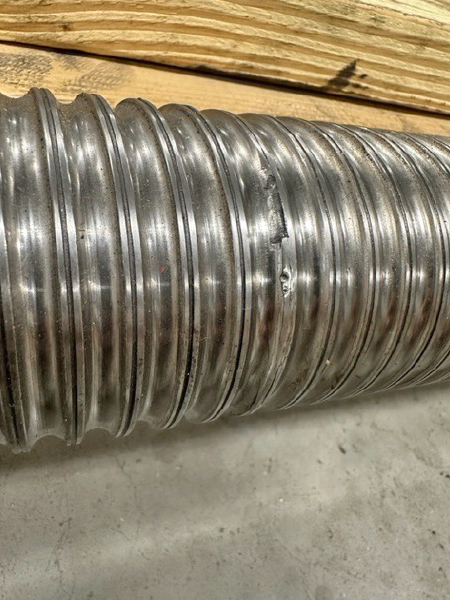
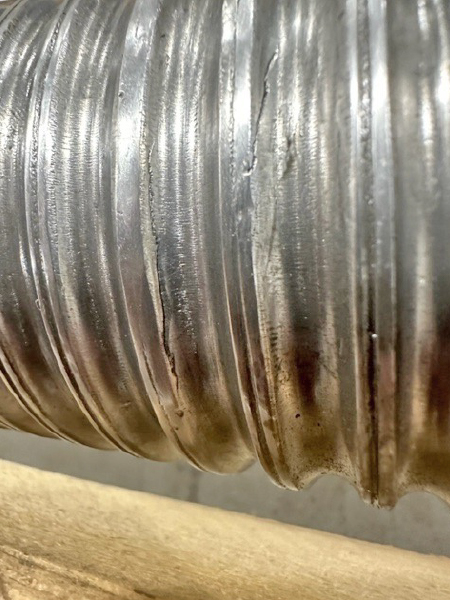
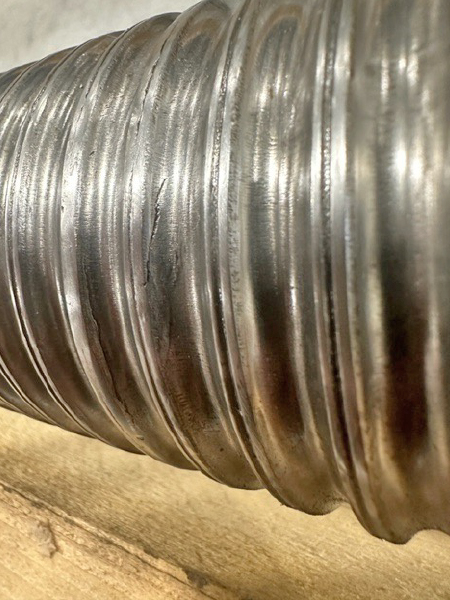
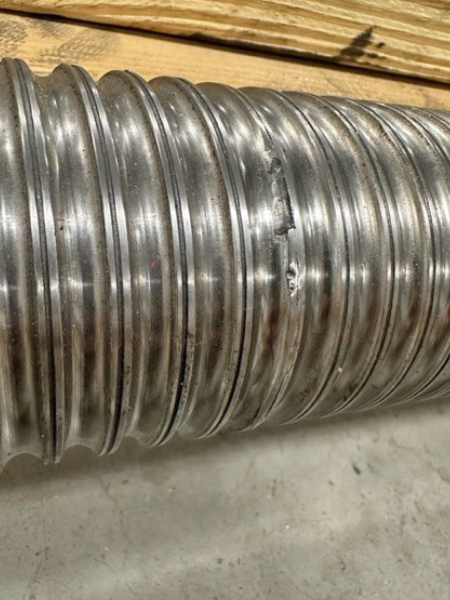
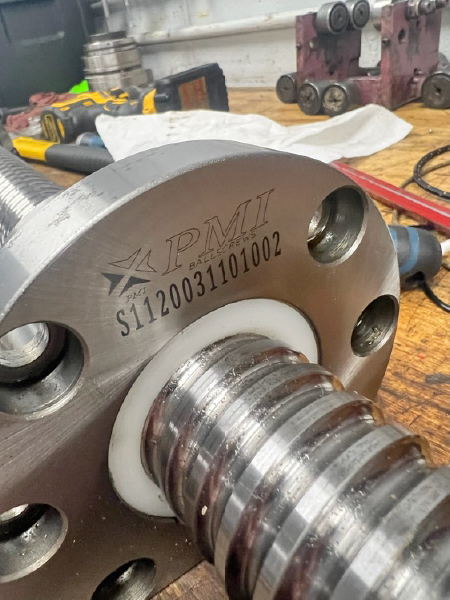
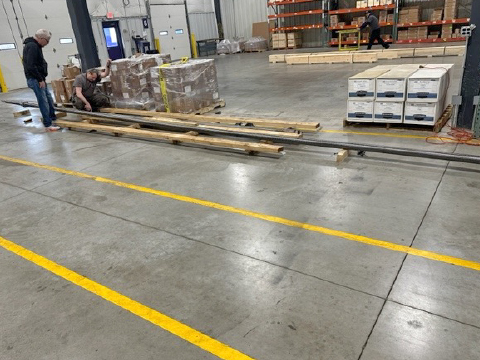
Learn more about our Service & Repair capabilities >